
Subsea Retrievable Modules
Flow Access Modules - FAM
FAM technology
Flow Access Module (FAM) technology fully aligns with fast track, low-cost subsea tiebacks, while still enabling the technologies required to maximize recovery from the well.
FAM achieves this via a patented FAM Flow Access Hub, which acts as a ‘USB port’ within the well jumper envelope. This supports the use of standard subsea architecture (XT, Manifold, PLET etc.) with FAM providing life of field flexibility within the system design.
The Flow Access Module is a retrievable package which can integrate various production optimization technologies, delivering functionality such as flow measurement, flow assurance, data acquisition and intervention access
Subsea Tieback
The drivers and benefits of Subsea Tiebacks are clear, enabling development of areas of oil or gas that might otherwise remain untouched. New wells can be tied back to existing subsea infrastructure, while keeping the environmental footprint to a minimum.
Short cycle times to first production, robust deliverability, and lower production costs lead to an extremely Capital Efficient solution in today’s environment.
Hunting’s Flow Access Modules provide the solution to optimize your subsea tieback.
FAM technology explained
Case Study 1 - Gulf of Mexico
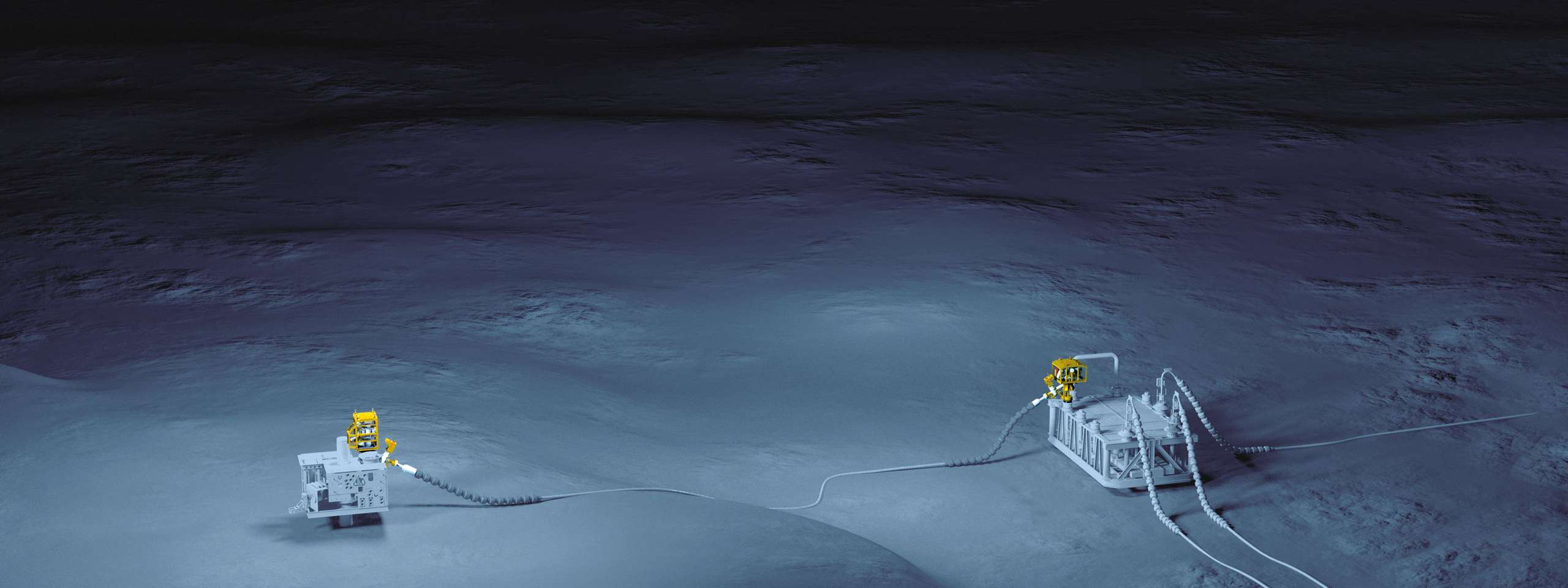
First installation of Flow Access Module (FAM)
In 2016, the first Flow Access Module (FAM) in Deepwater Gulf of Mexico was installed.
This early adoption of FAM was a contributing factor to the customer achieving a subsea tieback schedule of sanction to first oil in 11 months, a record for the Operator in the region.
FAM supported the use of a standard stock XT tied back to an existing subsea manifold. Moving the required project specific technologies (flow measurement and flow assurance) off the XT / manifold led to significant schedule improvement.
The Flow Measurement FAM at the XT end of the tieback incorporated an MPFM, WCM and ASD, by not having to build these into the XT allowed the use of a standard XT saving around 6 months of schedule.
The Flow Assurance FAM at the manifold end provided hydrate mitigation / management, supporting a longer step out distance to simplify drilling, and selection of single spur flowline instead of a dual flow loop, providing additional cost savings.
Case Study 2 - West Africa
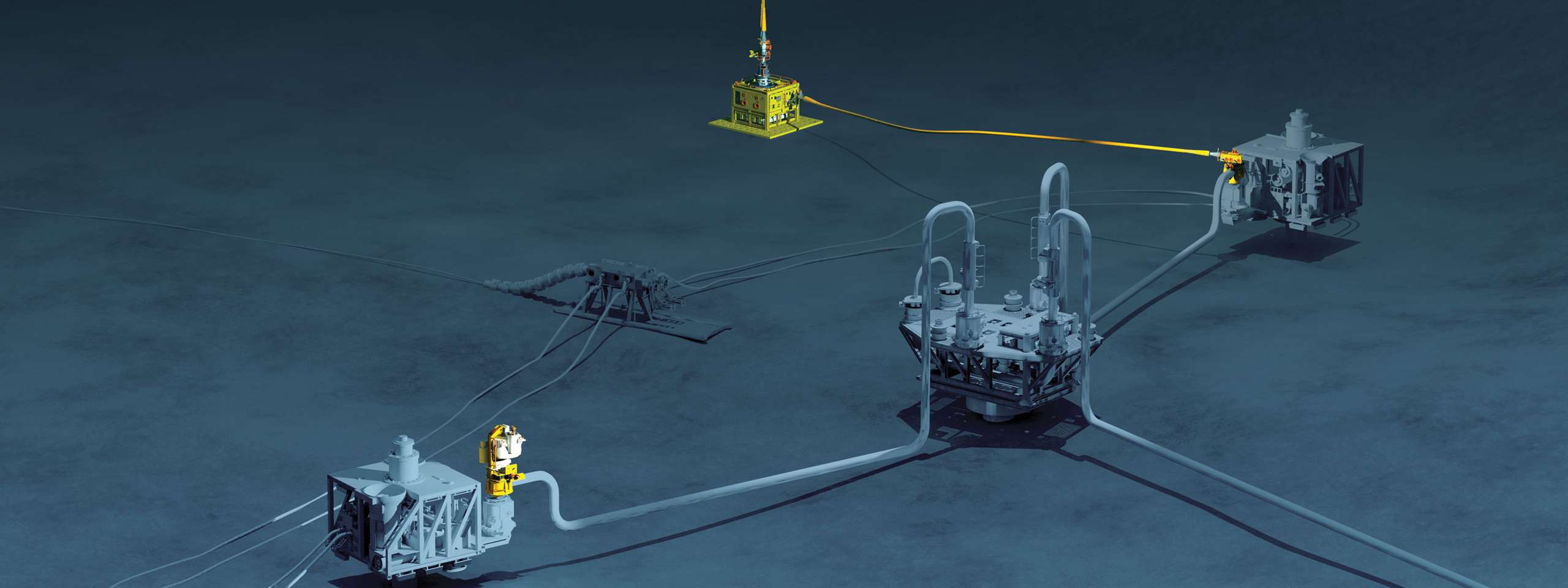
Project summary
Drivers
- MPFM technologies retrievable independently of rigid Jumpers
- Defer CAPEX costs
- Simplify Jumper fabrication and installation
Scope
- 10x Dual Bore FAM Hubs on Production Jumpers
- 5x Single Bore FAM Hubs on Injection Jumpers
- Brown & Green field
Case Study 3 - Gulf of Mexico
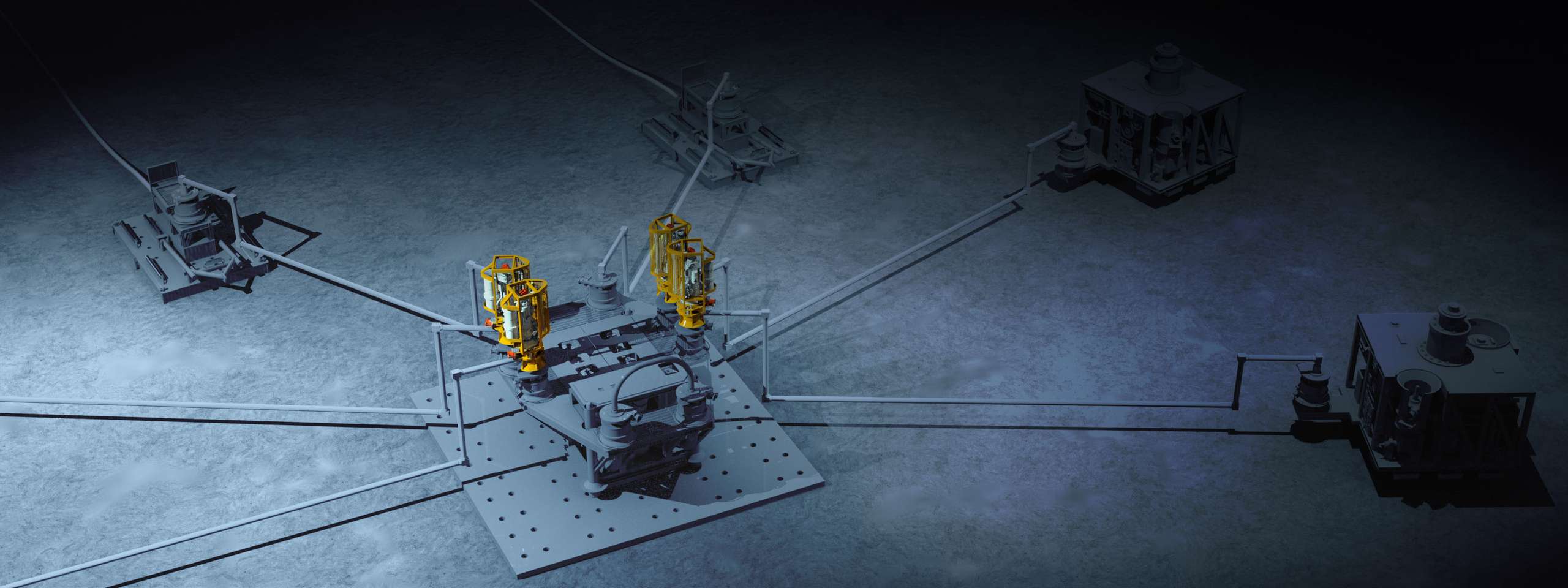
Project summary
Drivers
- Simplifies previous jumper design, removing fatigue concerns
- MPFM retrievable independently of Jumper
- Standard Hub design for 10k & 15k jumpers (future proof)
Scope
- 13x FAM with MPM Meters
- 10k & 15k Modules
- Manifold Location
Case Study 4 - Gulf of Mexico
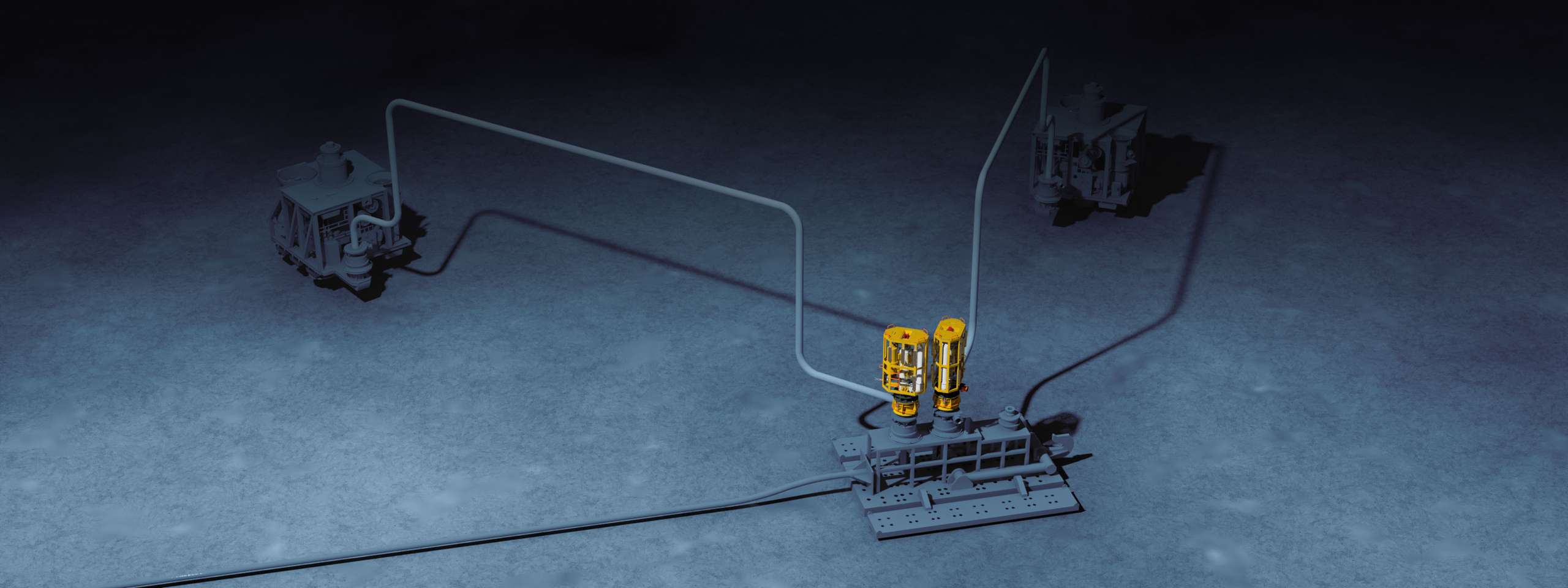
Project summary
Drivers
- MPFM retrievable independently of rigid Jumpers
- Simplify jumper and remove fatigue concerns
- Flexibility to incorporate latest MPFM model & legacy MPFM typesCopy / Bullets
Scope
- 2x FAM with MPM Meters
- 15k Modules
- PLET Location